Expanding the World’s Largest Refining Catalyst Plant
Turner Industries Reaches Milestone on Shell’s BlueCAT Project
Turner Industries’ Construction Division has reached a major milestone on the BlueCAT project at the Shell Catalysts and Technologies plant in Port Allen, Louisiana. After months of module assembly, the team is beginning to set its first modules on the project. These modules make up almost the entire expansion at the BlueCAT site and will further advance Shell’s environmental and production capacity goals.
The high-performance catalysts produced at the Port Allen facility are used to generate a less energy-intensive refining process and to manufacture biofuels and sustainable aviation fuel, among other products. The existing plant is the world’s largest refining catalyst plant, and this expansion will allow the facility to increase manufacturing capacity.
The project centers around the fabrication of 16 modules, set between elements of pre- and post-module stick built components. A unique element of this project is that, because of their height and the transport route into the plant, all but two of these modules are being assembled in the horizontal direction. They are then lifted vertically, in much the same way towers and vessels are raised in the vertical position. Designing, assembling, and securing modules to be erected vertically is extremely difficult and deserves recognition!
Turner and Shell have collaborated to develop an extremely strong BlueCAT execution team with a safety culture that is second to none,” said Shell Construction Manager Kevin Braud. “Assembling vertical modules in the horizontal position is already challenging, but modifying beams and connections after modules have been fully assembled adds a new layer of complexity that the Turner team met with a positive outlook. Stepping up to these challenges and continuing to execute with a flawless safety record gives us the confidence that this team will continue to perform at the high standard that they have set.
The original plan was to fabricate these modules at Turner’s 415 Module Yard in Port Allen. However, the team decided to build the modules onsite. With slight adjustments to neighboring land, Turner was able to bring on resources to construct the modules without increasing the project’s safety exposure hours.
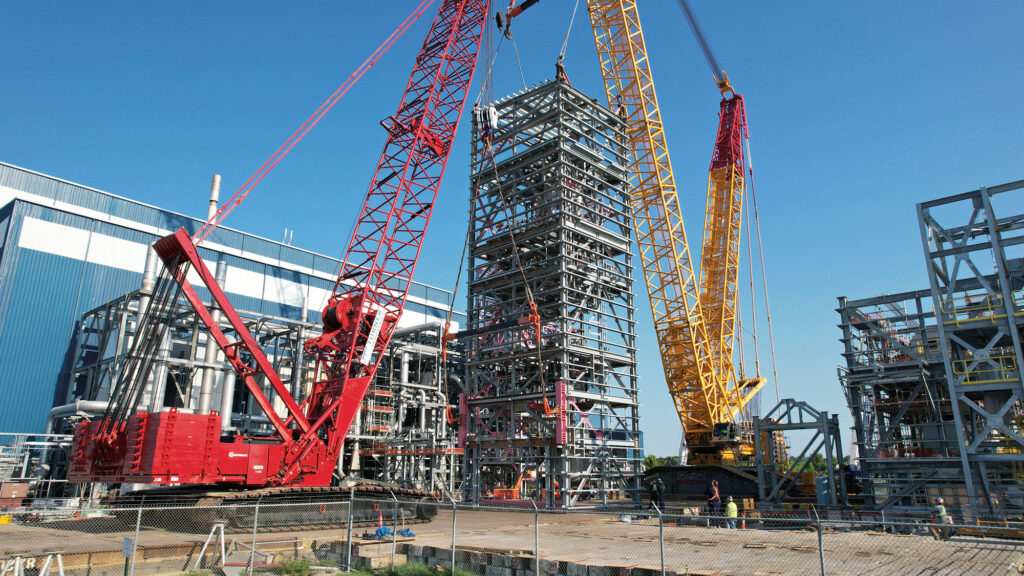
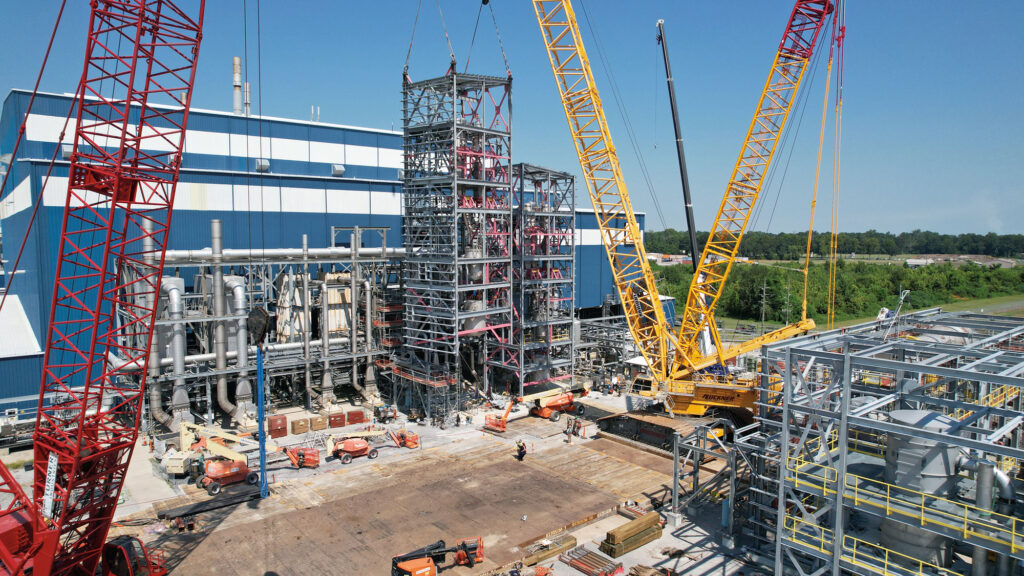
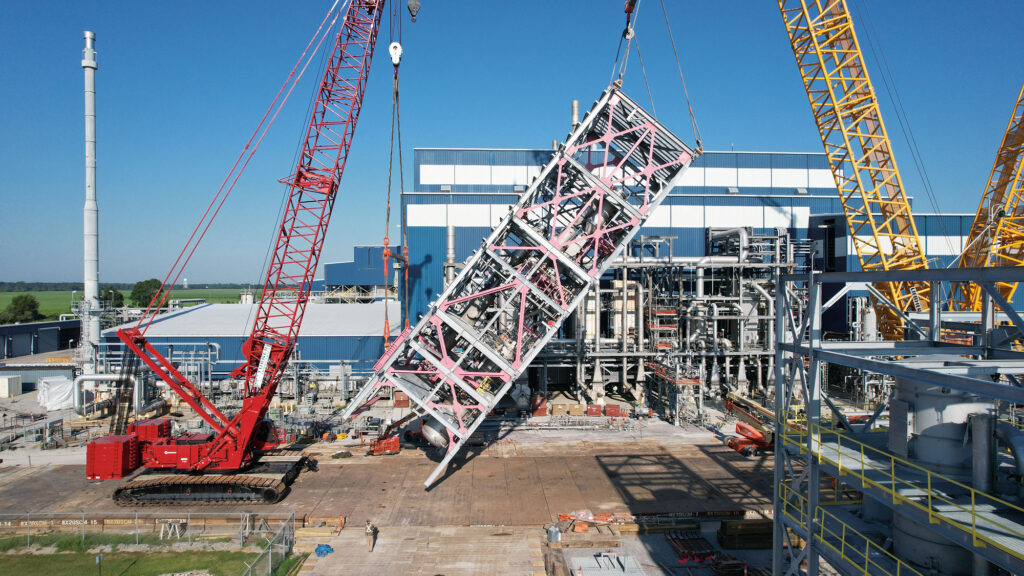
I could not be happier with our decision to partner with Turner for the construction of the BlueCAT project,” said Shell Project Manager Geno Tolari. “They truly perform as a partner in all aspects of their execution: excellent safety performance, quality, efficient work, and collaboration on issue resolution, to name a few. Turner has worked with Shell on other projects prior to this, and I continue to be impressed with the ownership and professionalism of their entire organization. I look forward to finishing this project strong together, and I hope to have the opportunity to work with this group again.
PROJECT QUICK FACTS
TURNER SERVICES PROVIDED
Pipe Fabrication
Modular Fabrication
Crane & Rigging
Scaffolding, Painting & Insulation
Environmental (Turner Specialty Services)
NDE (Turner Specialty Services)
EQUIPMENT
11 Process Modules
4 Stair Tower Modules
1 Piperack Module
3,800 Cubic Yards of Concrete
2,100 Tons of Steel
175 Pieces of Equipment
24,000 Linear Feet of Pipe